FATAR ファクトリー潜入レポート! 第3回:FATARの頭脳、技術開発部門に迫る!
- 2019/7/15
- インタビュー
- FATAR, Studiologic, インタビュー
前回は、FATARの技術が凝縮されたオリジナル・ブランド「Studiologic」のストーリーをお送りしましたが、お待たせいたしました! 遂にファクトリーに潜入です! これまであまり語られることのなかった、キーベッドができていく様子をレポートしていきます!
動画も交えながらお送りしますので、ぜひファクトリーの空気感を感じてください!
【これまでのレポート】
本レポートは、毎週月曜の12時に更新いたします。
製品開発の頭脳!開発部門に潜入
Marco:まずは技術開発部門から見ていきましょう。キーベッドの機構デザインなどを含め、FATARの製品はすべてこの場所から生み出されています。
これが製品のプロトタイプです。ご覧頂いて分かる通り、SL Mixfaceのパーツですね(笑)。本製造に入る前にプロトタイプを作成して動作をチェックするという工程を何度も繰り返していくのですが、今は3Dプリンターで作っています。
基板に関しても3Dプリンターで試作できるようになったおかげで、製品開発のスピードはかなり向上しましたね。
ここで衝撃の事実が判明します。
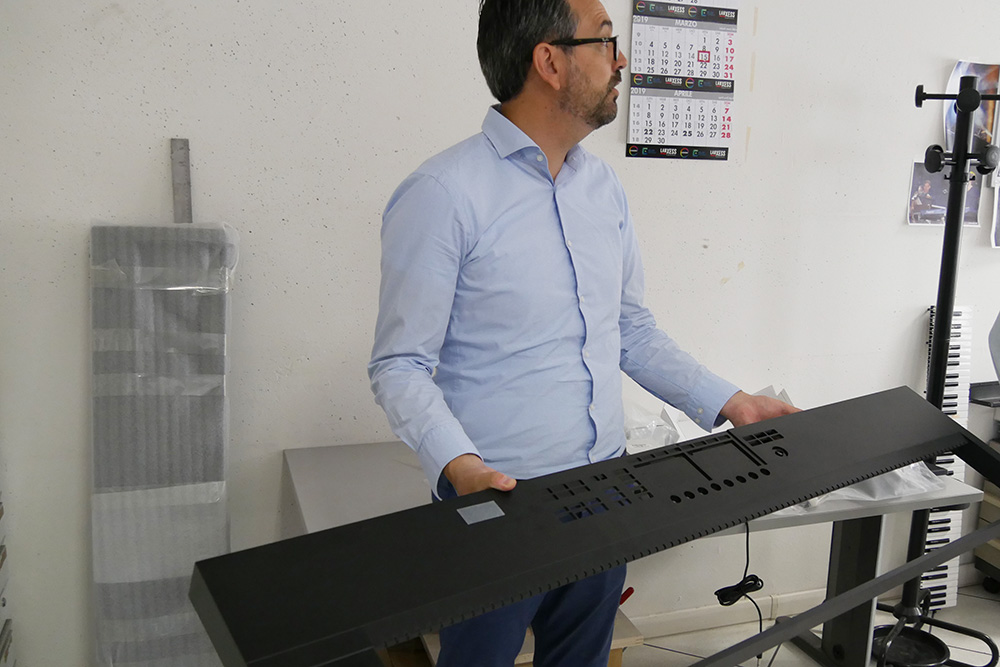
「これ、見たことない?」とMarco氏がおもむろに見せてくれたのは…。 DAWユーザーにお馴染みの、あの大ヒットMIDIキーボード・コントローラーのトップパネル!!!FATAR鍵盤が使われているのは知っていましたが、まさか製造までFATARで行われていたとは…。
Marco:このパーツ、どこかで見た覚えはありませんか? 大ヒットしているMIDIキーボード・コントローラーですが、このモデルの設計と生産はすべてFATARで請け負っているんですよ。この工場ではキーベッド単体や自社製品(Studiologic)だけでなく、様々なメーカーの製品を製造しています。これも私達の技術や品質が世界中で認められているからだと自負しています。
ピアノ鍵盤に隠された秘密が明らかに!
Marco:これはTP/400というピアノ・タッチのキーベッドですが、ご覧頂くと分かる通りプラスチック・パーツの周りを木材で囲むような設計になっています。確かにタッチを追求するならばすべて木製パーツを使うのが理想ではあるのですが、それにはデメリットもあります。気温や時間変化により反りや変形が起こってしまうのです。それでは長く愛用していただく楽器としては不十分だと私達は考え、メンテナンス性を含めたあらゆる面を総合的に考慮した結果、このような構造がベストだと判断しました。
プラスチックと聴き「演奏感は大丈夫なの?」と疑問に思われるかもしれませんが、ご安心ください。鍵盤タッチは私達が1番こだわっているところです。複数の素材を組み合わせたり独自の工夫を施すことで、木製鍵盤と遜色ないタッチを実現しています。
Marco:使用する木材についてもテストを繰り返し、ベストなものを追求しています。これはプラスチック・パーツに貼り付けたときに、どれくらい反りや歪みが生じるのかをテストしているところです。後ほど詳しく見て頂きますが、期間や環境を問わずに安心して使って頂けるような品質管理を徹底しているんです。
自作マシンが続々登場! 実証エリアに潜入!
Marco:では、ファクトリーに行きましょう。設計された製品は単に演奏感といった人間のフィーリングに頼るだけでなく、数値としても検証されます。まずはそのようなマシンからご覧頂きますね。
これは鍵盤の耐久性をテストするための機械です。新設計のキーベッドの場合、この機械に3週間…延べ300万回の打鍵テストが行われます。
ファクトリーにはこのような特殊なマシンが沢山ありますが、こういったものはすべてオリジナルで作っています。当然、市場で売っていませんからね(笑)。
次にこのマシンは、鍵盤の動きを計測するための機械です。取り付ける”おもり”を変えることでベロシティーを変更できるようになっており、例えばピアノをサンプリングするときには、ベロシティーいくつで鍵盤を弾くのか…という具合に使うことができます。
また出来上がった製品を、本物のピアノと同じ強さで弾いたときに、ちゃんと同じ音色が出るのかを確認・検証する作業にも使われます。
このマシンでは、温度と湿度の耐久テストを行います。キーベッドだけでなく、楽器そのものを中に入れて-25~65度の間で温度変化や湿度変化を与えたときの耐久性を確認します。
今は…温度40度で湿度が90%という状況ですね、ちょうど日本の梅雨や夏のような気候でしょうか? 同じように振動を与えたときの耐久テストも行います。これは日常生活というよりも、ファクトリーから楽器店までや、皆様のご自宅に向かうまでのトラック運送のシミュレーションですね。
続いて開発段階の製品を計測するためのマシンです。これを使うことで、鍵盤が何mm下がったときに、鍵盤にどの位の圧力が掛かっているのかを知ることができます。
圧力センサーはパソコンにつながっていて、動き始めから鍵盤の沈み具合をグラフに表示することができます。このマシンは日本の「イマダ」というメーカーのもので、とても精度と信頼性が高いんです。
ではこのグラフを見てください。横軸が鍵盤の動き(mm)、縦軸が掛かっている圧力を表しています。0から均等に圧力が掛かっていき、ちょうど1cm程度の場所で圧力が最大…つまり押し切った状態になっているのがわかりますよね?
次に、これがエスケープメント付きキーベッドのグラフです。ストンと落ちるような挙動をグラフで表すと、このような形になります。ピアノ・タッチのキーベッドを作る際には、これに似た機械を使って本物のピアノの鍵盤特性をグラフ化。同じようなカーブになるように細かく調整しています。
このように設計→試作→計測・検証の作業を繰り返しながら、FATARの製品はできあがっていきます。
次回は、プラスチックの射出成形エリアに潜入! 鍵盤や製品のボディーが生まれる瞬間をお送りしますのでお楽しみに!